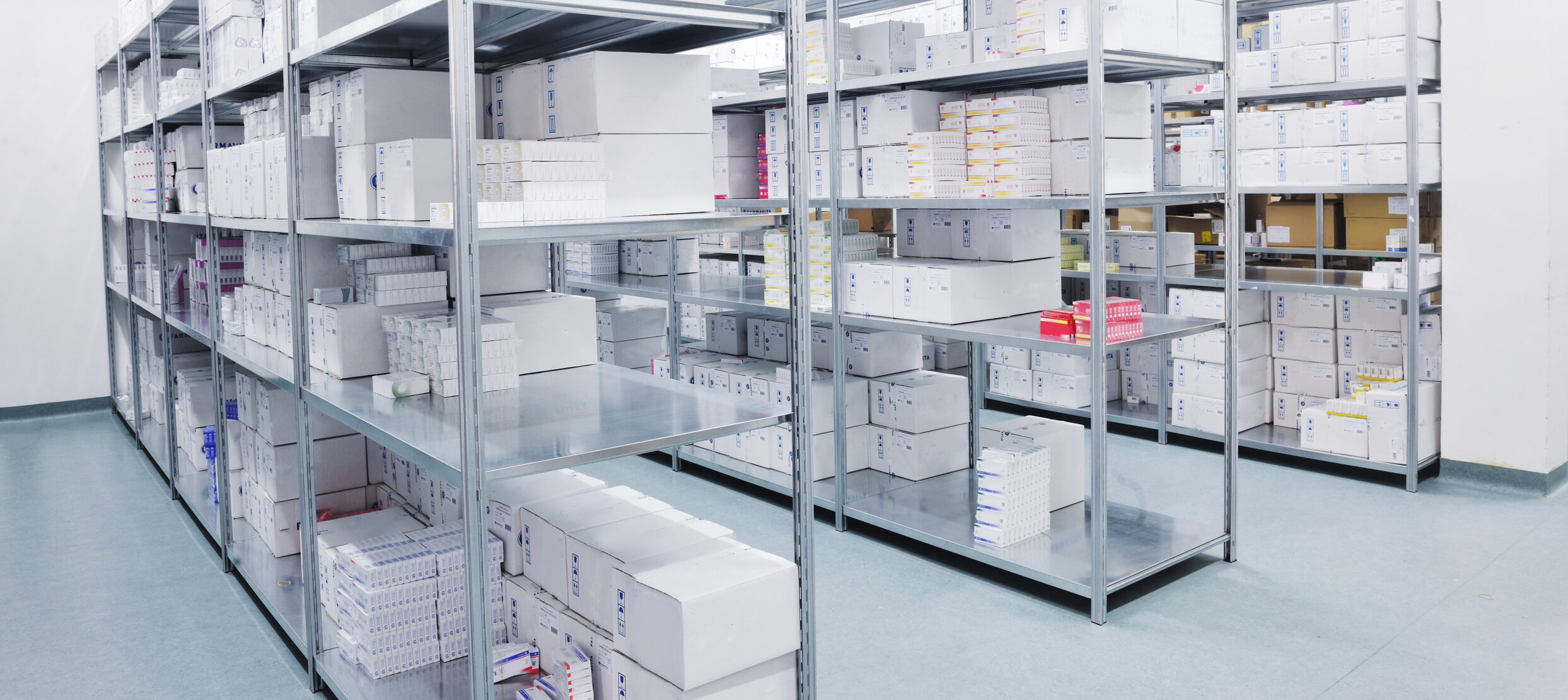
Technical service organisations cannot function effectively without a ready supply of spare parts to support service activities, whether in the field or in a workshop. It is one of the most critical aspects of service management, yet the one that is often managed poorly.
Having a proper spare parts inventory available to support service teams and customers is a balance between managing carrying costs and service efficiency. Parts are also used for training, support of internal loan and demonstration units, which also need to be kept in good working order.
Spare parts can include simple items like screws and tubes, to more complex components such as sensors and motors, to complex PCBs and expensive assemblies such as lasers and x-ray devices. Having the right parts available at the right time and in a condition that can be used by service teams is essential and should be a main focus of service management.
When spare parts are not available to service, service teams tend to engage in behaviour which undermines service efficiency:
- Parts are salvaged from decommissioned devices or incorrect repairs that misidentified parts for replacement.
- Parts are hoarded for engineers, disrupting stock control efforts.
- Parts go missing as salvaged and new parts are conflated by service teams further disrupting stock control efforts.
- Field service engineers engage in ‘quick-fix’ activities in an attempt to support customers while waiting for parts, but only reduce the reliability of the instrument, reduce customer satisfaction, and increase workloads on service teams in the attempt.
- Parts are scavenged from internal devices (loan and demo units) to get a customer device working, which is one of the worst decisions any service organisation can make. Not only does it risk additional damage to the instrument, it must be replaced with a new part when it arrives, making for additional workload and risk to both the customer unit and the original device the part was removed from, which now has additional reliability risk.
There are several things to consider when it comes to effective spare parts management:
Availability
- Minimises downtime, a key customer metric in any service organisation.
- Requires a robust and efficient stock management system to track parts usage and anticipate service needs, while avoiding overstocking.
- Requires an efficient logistics and distribution process to ensure parts are delivered quickly to customers and service teams as needed.
Quality and Reliability of Parts
- Only use new, genuine, manufacturer-approved parts to ensure compatibility and reliability.
- Strict quality control measures ensure parts that are provided are correct, will work as expected, and are free of defects.
Correctness and Compatibility
- Ensuring parts match the exact technical specifications of the equipment is essential to avoid damage and ensure reliable performance.
- Detailed documentation must be available describing correct use and replacement of a part to ensure service teams reduce mistakes during replacement and adjustment.
Cost Management
- Balancing the cost of maintaining a comprehensive inventory against the financial impact of downtime and emergency shipments is essential. Negotiating favourable terms with suppliers can also reduce costs.
- For field service, the most significant manageable cost is unplanned service visits, which are reduced significantly with effective parts availability.
Training and Knowledge Sharing
- Regular training programs for service engineers on the latest equipment and parts ensure they are prepared to handle repairs and replacements efficiently.
- Salvaged and failed parts do have a place in service. These parts are excellent resources for training service engineers on the parts, common issues, and service tricks and tips. This reduces training costs and the burden on stock management for new parts.
Customer Satisfaction
- High availability and quick turnaround on parts contribute significantly to customer satisfaction.
- Demonstrating a commitment to using only new and genuine parts builds trust and establishes the organisation’s reputation for reliability and professionalism.
Technology
- Advanced inventory management systems, such as automated tracking and forecasting tools, are less effective when it comes to spare parts availability.
- These tools do not take into account the sporadic demand of critical but slow-moving parts without manual intervention. Additionally, a lack of available parts can create a knock-on effect in supply issues.
- Managing levels of spare parts is a calculation that needs frequent attention and must be forward-looking.
- The more effective the service team is at identifying problems and improving reliability, the more predictable spare parts planning becomes.
Supply Chain Resilience
- Developing contingency plans and maintaining multiple suppliers for critical parts can mitigate risks associated with supply chain disruptions.
- Parts availability is dependent on having a clear view of parts usage and needs from production all the way down to the end user and having the systems in place to meet that need.
Customer Education
- Educating customers on the importance of only using genuine parts and the impact of poor-quality substitutes can lead to better customer interactions, as well as more reliable instruments.
- Being transparent about parts usage and costs in service agreements can build trust and prevent misunderstandings.
With these considerations in mind, it is highly recommended that spare parts levels are controlled by the Service Team, whether that is as a separate stock entirely, or a subset of a main warehouse.
The simplest and most effective model for managing inventory is the basic Min-Max system. If stock levels of a part fall below a specific target (Min), an order is generated to restock inventory at the Max level.
Managers can adjust levels as needed with regular reviews of stock needed, upcoming service activities (such as upgrades, recalls, seasonal maintenance, promotions, etc). Levels can also be adjusted to close to equilibrium states once service delivery is highly efficient and service activities are proactive more often than not.
To reiterate, spare parts management is one of the most critical functions impacting service efficiency and must be a priority of service management.
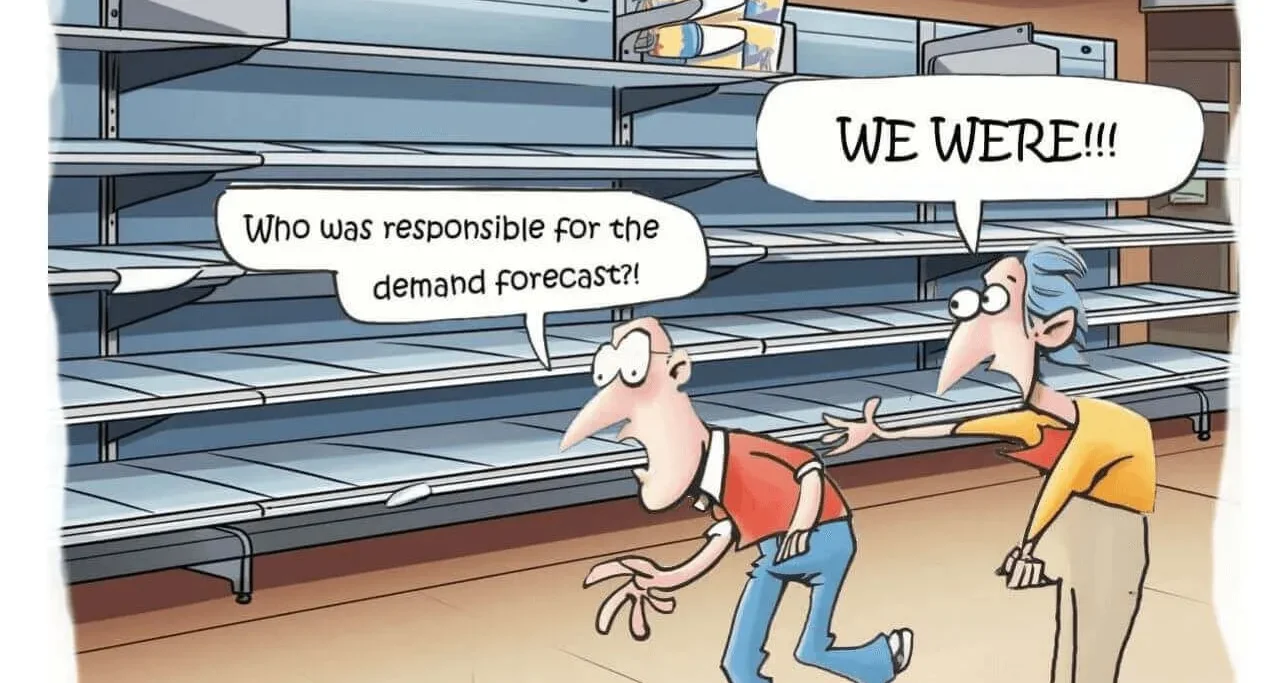
If you would like help in managing your spare parts availability, contact Creekline Consulting